Unveiling Thunderbird’s 40-Year Legacy in Injection Molded Plastics
Since its founding in 1976, Thunderbird Plastics has undergone a unique and admirable business journey. After a decades-long buyout process, the company finally landed in the hands of the Nucera family where it lovingly stays today. With an expansive product lineup of high-quality injection-moulded HPDE plastic industrial products, Thunderbird is much more than a product manufacturer. At Thunderbird, you can approach them with an idea and be granted access to a team of engineering professionals ready to lead you through the design, prototyping, and production process to bring your idea to fruition.
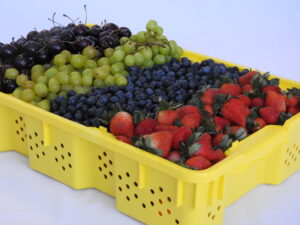
Thunderbird’s Berry Lug
As Thunderbird Plastics approaches its fifth decade in operation, we look back on product offerings and the technology that shaped it, we celebrate Thunderbird’s impressive dedication to sustainability, and finally, we look at the impact that Thunderbird has had on the community both on the individual level and in the small/medium business sector.
Decades of Innovation: Shaping Thunderbird’s Product Lineup
In Thunderbird’s first decade of operation, the primary manufacturing technology for the Thunderbird products lineup was injection molding with the company keeping up with the latest technology available in the 1980s.
Aided by up-to-date machinery and Giuseppe Nucera’s previous plastics manufacturing experience of making plastic crates in Italy, the 1990s product profile saw an expansion into canning sleeves for the construction industry as well as designs tailored to the agricultural sector.
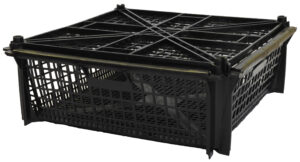
Thunderbird’s Oyster Growing Tray with Optional Lid
With strong plastic milk crates and plastic garbage cans still a staple offering in this decade, the late 1990s saw another expansion of products intended for use in oyster farming and the aquacultural industry broadly such as fishing baskets and plastic cages.
The investment into machinery and product design paid off in the 1990s with Thunderbird Plastics doubling in size in many ways.
Physically, the company found itself short of storage space, prompting a decision to rent a nearby building for storage space. Quickly seeing and seizing an opportunity, Giuseppe Nucera opted to buy the property instead with support from to-this-day manager Mario Bottazzini.
Nucera, in his 60s at this point, would see this bold move lead to growth as more space meant more product storage.
Thunderbird’s product offering, and more so its evolution, reflects an enduring flexible strategy that adeptly navigated circumstances and opportunities across southern BC. While dairy crates and plastic bins remained one of Thunderbird’s core revenue drivers, the agricultural surge, particularly in the late 90s with the Washington oyster industry, boosted company revenue significantly for over a decade. Production output was able to meet the demands of this industry due to a flexible strategy and available resources. Additionally, a flexible strategy was helpful when some products that had been initially designed for one purpose found unexpected success in entirely different markets.
Thunderbird Plastics was able to focus on investing in expanding its design capabilities, with an optimized product line and modern machinery facilitating efficient production.
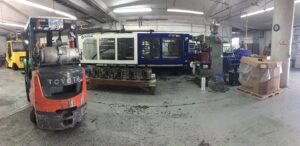
An inside look at some of our production equipment.
Nowadays, Thunderbird boasts a steady flow of sturdy and cost-effective industrial products including berry trays, fisherman baskets, lug containers, plastic pallets, and much more. Throughout the last nearly five decades, Thunderbird has evolved to have an impressive ten production lines. Despite previous experiences and technical know-how in both plastics extrusion and blow moulding and exploration of rotational moulding, injection moulding continues to be the sole method of production at Thunderbird due to increased output capabilities. Notably, the injection molding method is the same technology used by Lego to manufacture their popular children’s toys.
In addition to impressive output capabilities of 2 million items per year, Thunderbird is able to make products with an impressive range in size. Along the production line, there are presses ranging from 350 to 2250 tons that allow Thunderbird to create items weighing only a few grams up to 9 kilograms.
Sustainable Practices: Thunderbird’s Commitment to the Environment
While high-quality injection moulded plastic products became the core of Thunderbird’s business, the plastics industry itself was not earning a favourable reputation. This reputation was in large part due to the plastics industry as a whole failing to plan for the entire lifecycle of products and allowing their industry waste to cause harm. In the last few decades, society has become increasingly aware of the dangers of irresponsibly discarded plastics polluting our lands and waterways and many eco-conscious groups have lobbied to ban single-use plastics. Contrary to the industry’s previous inattention to the end-of-life cycle of a plastic product, Thunderbird blazes a trail by claiming responsibility for their products throughout their entire lifecycle. Furthermore, they offer each customer the participation in a recycling program in which end-of-life products are taken back by Thunderbird to make new products.
Thunderbird’s sustainability journey began in the early 2000s, long before plastic had earned its poor reputation when the company embarked on an initiative that highlighted its dedication to the environment and the community by agreeing with local municipalities to recycle their roll carts at the end of their life cycle – at no cost. Thunderbird showed their dedication to sustainability in plastics by modelling their behaviour by their core values and offering a positive solution to both taxpayers and environmentalists. An impressive dedication to walking the walk endures to this day as the free recycling agreement remains in place with the local municipalities.
Thunderbird is a shining example of how both plastics manufacturing and recycling can be both economically and environmentally sustainable, much more so than consumers may realize.
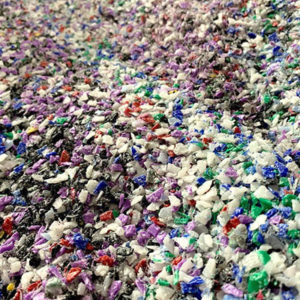
Materials after the wash-and-chop process, ready for moulding again.
The alignment between consumers and corporations concerning the roles and responsibilities regarding plastic disposal is very important. With sustainability at its core, Thunderbird Plastics is committed to educating consumers on the correct recycling processes for their products.
Thunderbird exclusively uses manufacturing materials that are 100% recyclable, and they ensure to only use materials that can be made into new Thunderbird products. Every scrapped item that they produce is recycled through their “wash and chop” system.
Innovative Synergy: Thunderbird Plastics’ Decades-Long Commitment to Knowledge, Innovation, and Adaptability
At Thunderbird Plastics the evident intersection of knowledge, innovation, and adaptability within every decade of business is apparent. With his informed approach to business, Giuseppe Nucera has imparted a legacy at Thunderbird in an enduring way. Keeping with this theme today, Thunderbird offers the business community and innovative minds the opportunity to access machinery and engineering professionals who can help bring a concept to fruition.
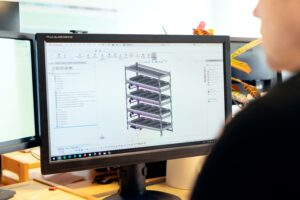
The Thunderbird team helps you go from concept, to 3D prototype, to final product.
A cherry-picked team of in-house design and engineering professionals helps you assess the performance of your designs in real-world applications. Keeping a systematic and yet innovative approach has been a significant enabler for new projects and business partnerships.
Beyond the existing plastic baskets, plastic crates, plastic storage bins, plastic totes, and plastic bins for sale – Thunderbird welcomes enterprising clients to collaborate and design their own plastic boxes for packaging, plastic carrying cases, or plastic packaging. Much more technical designs have been created with Notable clients who have collaborated with Thunderbird Plastics in designing and prototyping a product from concept to production.
Since 2019, Thunderbird has been using 3D printing for rapid prototyping. After acquiring an FDM Printer, Thunderbird capabilities expanded to create smaller-scale 3D prototypes. Unlike 3D print shops, Thunderbird uses these smaller-scale prototypes as part of a product development process. This capability has been well received with customers, as it adds a real-life tactile perception to computer-generated 3D models during the design phase.
Sustainable Horizons: Thunderbird Plastics’ Vision for Environmental Leadership and Community Commitment
Thunderbird envisions a future in which they continue developing sustainable environmental practices while continuing to engage with the community through initiatives like free recycling for local municipalities. They currently give back to the community through sponsorships for farming education and sponsorships that support farming associations in the development of new farmland. In a heartwarming display of decades-long corporate responsibility, Thunderbird Plastics invests into the community in a way that parallels the multigenerational investment into the company by the Nucera family. A company that looks at the future beyond offering plastic boxes for sale is a company that is built for longevity.